A quick overview of the common issues
By Shiyi Chen, M.Sc., M.Eng., EIT
Over the past few decades, the utilization of plastics in manufacturing has witnessed a remarkable surge, owing to their inherent advantages over traditional metal counterparts. Plastics, with their lighter weight, enhanced durability, and resistance to corrosion, have emerged as a compelling choice across a myriad of applications, ranging from household appliances to cutting-edge medical devices. Nonetheless, delving into the intricate world of polymer failure analysis reveals a realm that is far from well-understood, unlike the extensive knowledge surrounding metal failure mechanisms. The multifaceted molecular structure of polymers gives rise to a diverse array of failure modes, including creep, stress relaxation, and environmental stress cracking. Consequently, conducting a thorough examination of polymer failure necessitates specialized expertise, equipment, and methodologies distinct from those employed in metal failure analysis.
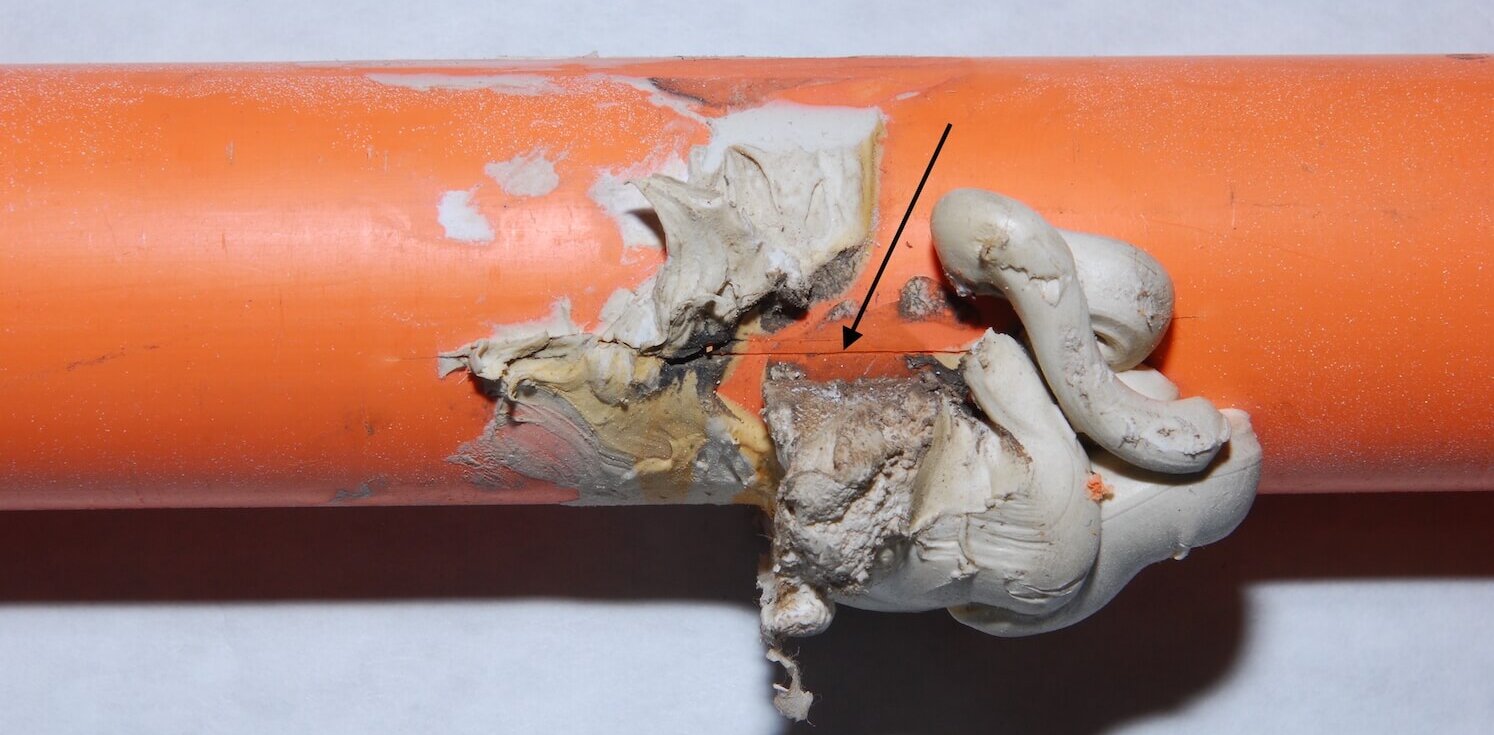
The root causes behind polymer component failures generally trace back to one or more of the following issues: inappropriate design, manufacturing defects, or flawed installation practices.
Inappropriate Design and Polymer Failure Analysis
In the realm of polymer failure analysis, inappropriate design stands as a prevalent challenge. Notably, stress risers, areas within a component that are particularly susceptible to stress concentration, pose a significant concern for notch-sensitive plastics. These are plastics prone to failure when subjected to stress concentrations, often arising from notches, sharp corners, or thread roots. For instance, CEP has encountered numerous instances of coupling nuts on flexible hoses failing due to elevated stress levels acting upon sharp thread roots. By avoiding stress risers or incorporating design elements with smooth transitions and rounded corners, designers can effectively mitigate the risk of polymer failure, ensuring that plastic components perform their intended functions reliably.
“ Additionally, a mismatch in material selection or overlooking environmental factors can precipitate polymer failures. For example, the utilization of linear low-density polyethylene (LLDPE) for transporting chlorinated water can expedite the degradation of LLDPE pipes, resulting in premature failure. ”
Manufacturing Defects and Polymer Failure Analysis
Manufacturing defects wield substantial influence in the realm of plastic component failures. Voids and inclusions, introduced during the manufacturing process, can serve as stress concentration points that initiate cracks and eventual failures. In injection-molded parts, weld lines or knit lines represent another common initiation site for cracks.
These defects materialize when two or more flow fronts converge and create seams within the part during manufacturing, establishing weak points with reduced strength and stiffness, rendering them more susceptible to failure.
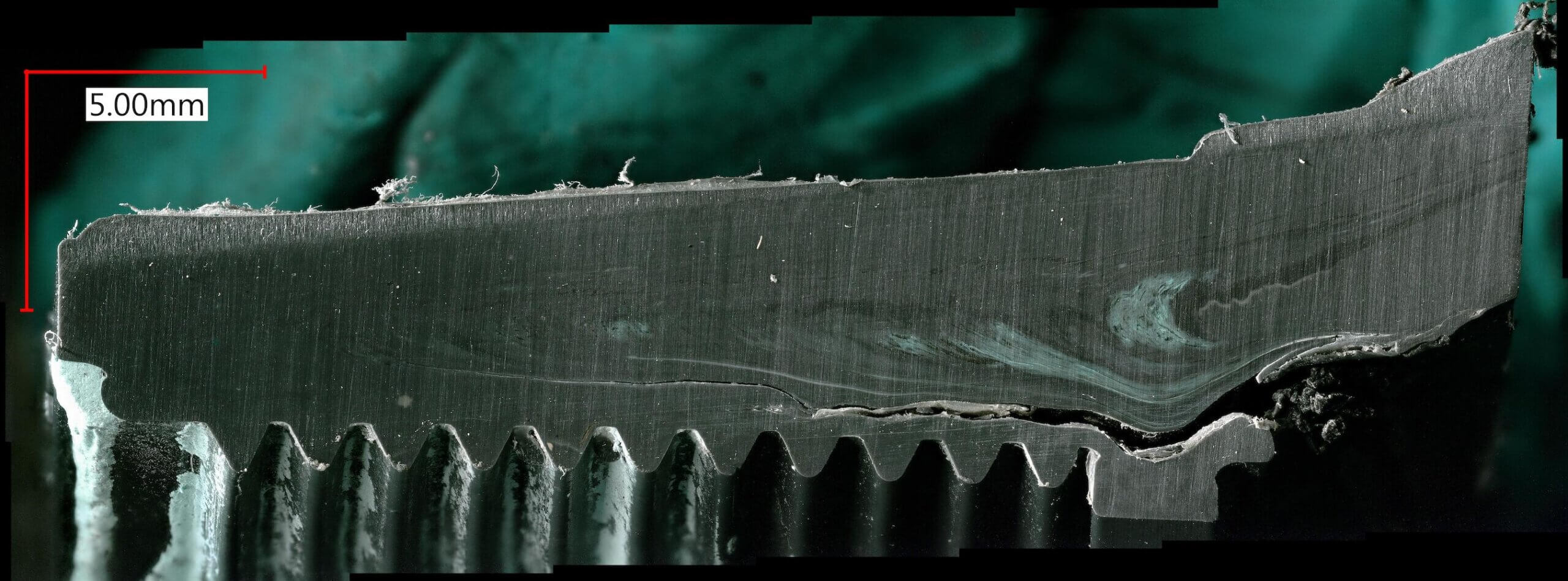
Installation-Related Polymer Failure Analysis
Challenges related to the installation of plastic components are pervasive. This category encompasses instances of improperly calibrated tools and mechanical damage to components during installation. Unlike metals, plastics possess weaker internal forces holding their structure together, making them vulnerable to long-term failure mechanisms, such as crazing, induced by excessive stress during installation. Crazing manifests as the formation of small, often microscopic, cracks or fissures in plastic components. These imperfections may initially go unnoticed, and the component might appear to function correctly. However, over time, these cracks can propagate and ultimately culminate in catastrophic failures. Historical cases have showcased plastic fittings and piping failing due to inadequate support months or even years after installation.
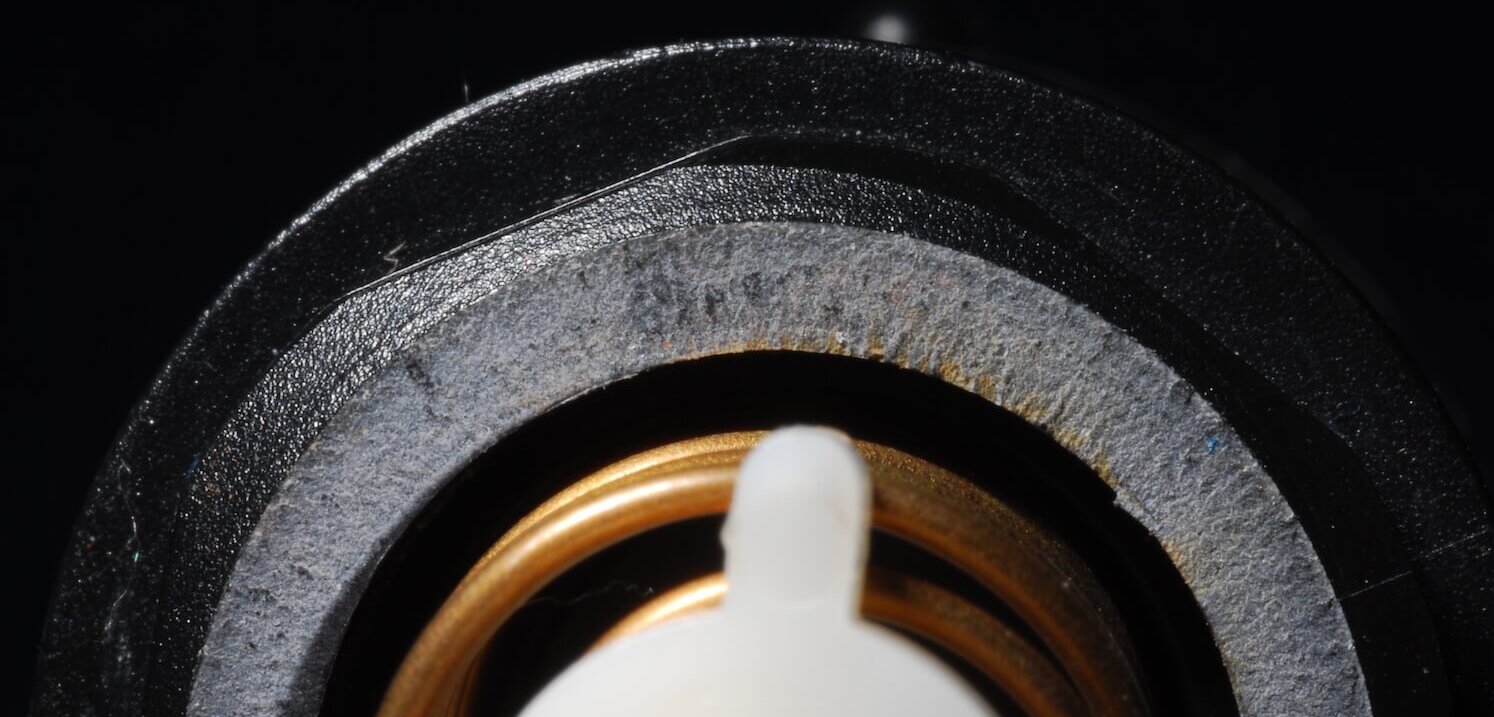
To prevent such failures, it is imperative to adhere to installation guidelines outlined in the product manual and local building codes diligently. Notable examples of installation issues include nails puncturing flexible water supply lines or the improper use of uncalibrated crimping tools on PEX pipe fittings.
When conducting product failure analysis, forensic engineers must have a comprehensive understanding of these facets which are indispensable for ensuring product integrity and reliability in an era where plastics play an increasingly pivotal role in modern manufacturing.
Following a failure, a comprehensive examination and analysis should be completed to identify all contributing factors. At CEP, we have experts that are specialized in forensic failure analysis for plastic components. Our team of experienced engineers and scientists uses state-of-the-art equipment and techniques to identify the root cause of various product failures. To talk about a claim with one of our experts, contact us.