Are you familiar with NPT (National Pipe Taper) joints? The term may not mean anything to you at first, but it is a configuration of threaded joints in metal piping commonly used for more than 100 years. NPT joints ensure leak-tight connections between sections of metal piping that supply water, fuel, or gases to different systems, whether for drinking water, fire protection systems (including sprinkler piping), or heating systems. This article provides an overview of the basic engineering concepts associated with NPT joints and debunks some myths.
Offered in a wide variety of sizes, depending on the required use, NPT joints are widely used because they allow permanent and durable connections to be made using hand tools, without the application of heat, and without the use of gaskets (or O-rings). NPT joints can be used in all types of metal piping but are most often found on parts made from steels, cast irons, stainless steels, or brasses (an alloy of copper and zinc).
The B1.20.1 standard of the American Society of Mechanical Engineers (ASME) specifies the requirements for NPT joints. While B1.20.1 provides specifications for NPT joints for piping up to 24 inches in diameter, these types of connections are mainly used for piping diameters of 2 inches or less.
Assembly
One of the critical features of NPT joints is that the engaging threads are tapered. During tightening, a slight deformation is generated by “metal on metal” contact, resulting in a leak-tight connection.
The assembly of an NPT connection is done in two steps per ASME B1.20.1. First, the connection is screwed in (tightened) by hand for the first four threads. Subsequently, a tool, such as an adjustable wrench, is used to tighten the joint until it is fluid or gas tight. As the tapered threads result in a conical seal between the engaged components, the friction (and therefore deformation of the threads) increases as the connection is tightened, resulting in a tighter seal. It is also generally necessary to use PTFE tape (teflon) or paste (pipe dope) to lubricate the threads and to fill small gaps, thus ensuring a complete seal.
In tightening an NPT connection, the number of turns to be made with the tool depends mainly on the diameter of the connection and the internal pressure to be sustained. For piping sizes of 2 inches or less, ASME B1.20.1. specifies a maximum tool tightening of three threads. For low pressure applications, a tightening of 1.5 to 2 threads using a tool is often sufficient to ensure a tight connection. In this sense, it is relatively uncommon for these types of connections to be overtightened based on the requirements of ASME B1.20.1.
It is preferable to use NPT joints for permanent installations, where they will not have to be repeatedly assembled and disassembled often. Frequent assembly and disassembly results in wear of the threads, compromising the tightness of the NPT seal.
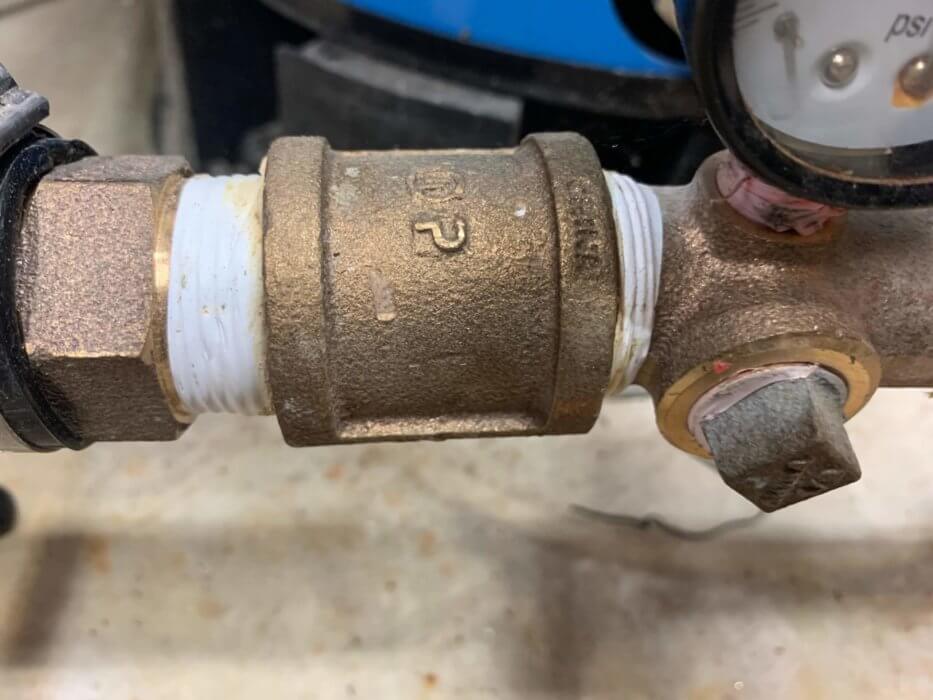
Typical plumbing NPT joints with Teflon tape
Additionally, if NPT joints for industrial applications are not sufficiently sealed, they can often be repaired by soldering using procedures specified by ASME PCC-2 or NBIC NB-23, Part 3.
Similar Seals
There are also similar connections, such as NPTF (National Pipe Thread Fuel) that can be used when it is not possible or recommended to use tape or paste. These are, however, less common, and more expensive. There are also NPS (National Pipe Straight) joints. Unlike NPT seals, NPS seals must be gasketed.
Summarizing Thoughts
In short, each method of connecting piping and fittings has its advantages, disadvantages, and limits relating to the temperature and pressure of the liquids or gases circulating in the piping of the system they supply, and their ease of assembly, maintenance, and susceptibility to leakage or failure.
However, for NPT connections, if there is a lack of tightness, this problem usually appears immediately and is generally caused by under tightening, threads that do not have the required tolerances, or the improper use of paste or tape. Where a failure occurs, this is more typically related to the manufacturing or selection of the part rather than other causes. It should be noted that connections in larger diameter pipes are generally more difficult to seal, since the joint area is much larger than those of small diameter.
A Few Myths
CEP Forensic is often called upon to analyze NPT seals in claims files, such as water damage. We find that some myths still persist today. Let’s unbolt a few!
Myth: Tool marks on the pipe or fitting indicate that the joint has been overtightened.
Reality: There is not necessarily a causal link between tool marks and overtightening since the presence of marks depends mainly on the choice and adjustment of the tools. Experience and laboratory testing have shown that a badly worn fitting may be under-tightened, while a very tight-fitting may show almost no marks. Damaged parts may indicate a home installation but have no direct relationship to the tightening force. Looking at the number of threads engaged is a much more reliable method of determining the quality of the installation.
Myth: An overtightened fitting can crack several weeks or months after installation due to improper assembly
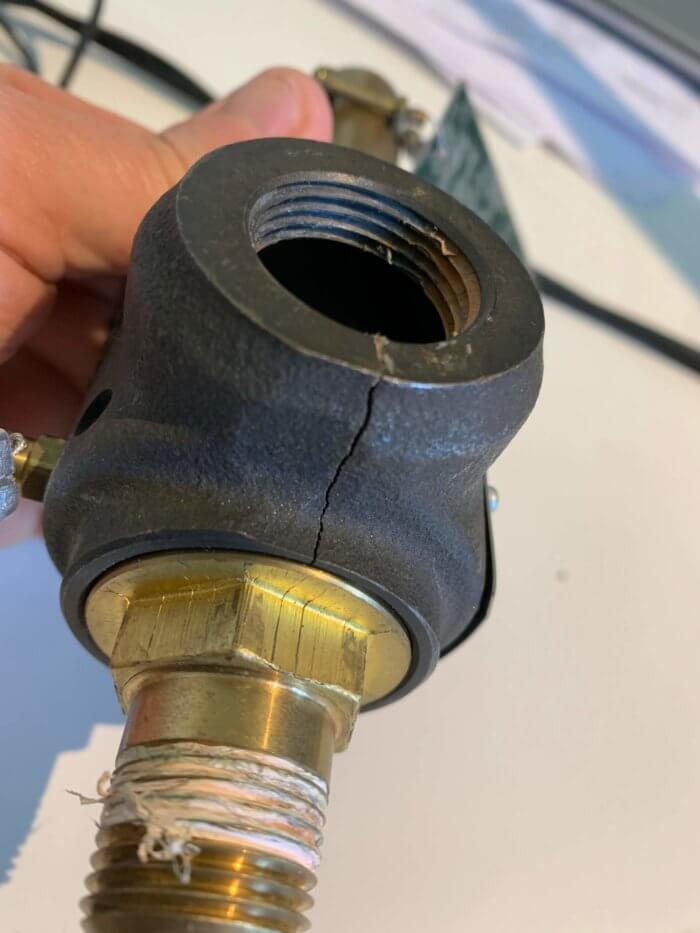
Breakage while tightening
Reality: Where an NPT joint is tightly connected, the parts can sometimes break, especially when the female-threaded part is made of gray cast iron, a brittle alloy. In such cases, this breakage typically occurs immediately or very shortly after installation. Delayed breakage of components of NPT joints generally affects brass components in networks carrying water. This type of breakage is generally found to be related to stress-corrosion cracking (SCC) of the brass and not simply attributable to overtightening. This type of breakage is seen more often on the female-threaded fittings in NPT joints since the conical configuration of the connection puts the female-threaded part in circumferential tension while the male-threaded part is put in compression. This type of breakage is therefore generally caused by a manufacturing or design issues affecting the brass component(s) and not by improper installation.
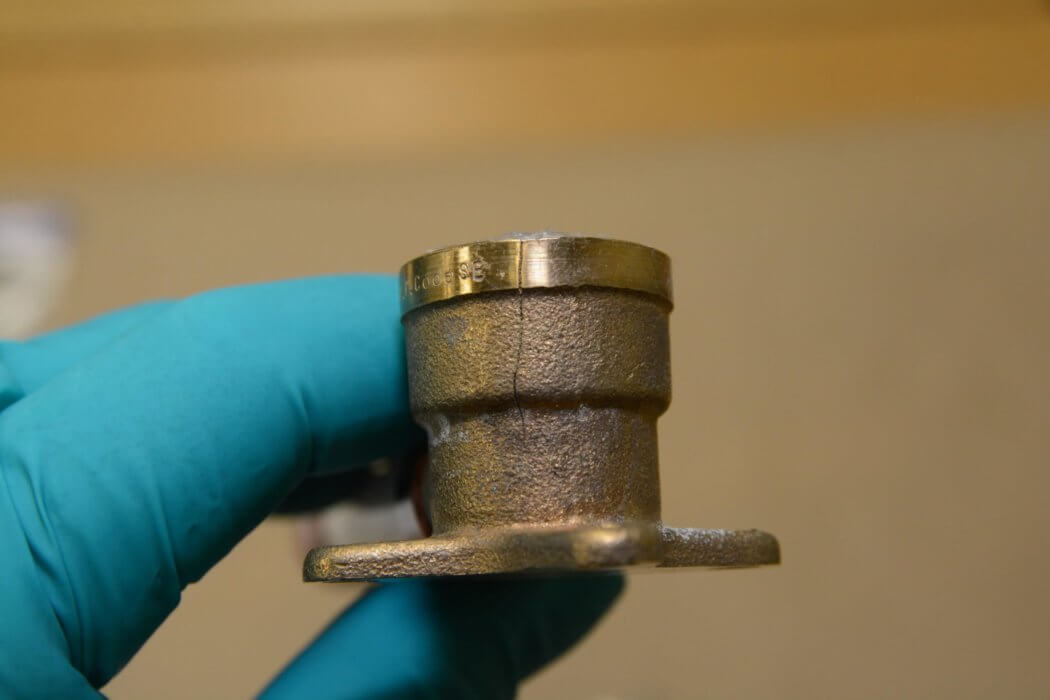
Breakage a long time after installation
Myth: NPT fittings should be installed using a tightening torque value that should be specified by the designer.
Reality: Unlike bolt installation, where torque is commonly specified for the installation, ASME B1.20.1 states that it is not possible to specify these values for NPT joints due to material variations, wall thickness, operating pressure, etc.
As discussed above, a tight joint resulting from between 1.5 and 3 threads (complete turns) using paste or tape is normally sufficient to ensure a tight seal without the use of torque values. It should also be noted that some adjustment in NPT joints is sometimes necessary, for example in the case of 90-degree elbows which must be oriented in the right direction.
Myth: PTFE (Teflon) tape electrically insulates parts and acts as a dielectric joint.
Reality: When two metals are in contact in a corrosive environment, an accelerated corrosion phenomenon (galvanic corrosion) can affect the more chemically active material. A common example of this is the rapid corrosion of galvanized steel water pipes when connected directly to copper or its alloys. To avoid this, an insulating (dielectric) joint must be used to electrically isolate the two metals. That said, PTFE tape cannot act as such an insulator since it is highly deformed when tightened and does not completely prevent metal-to-metal contact. A simple continuity test with a multimeter can confirm this.
Notably, in the case of water that is deoxygenated or treated with corrosion inhibitors, such as a sprinkler or heating system, the use of a dielectric fitting is generally not necessary as the liquid is not corrosive. However, CEP has worked on several files where the failure of a steel-brass NPT joint occurred due to a small leak that went unnoticed. Due to this leak, the outer threads of the joint were then in contact with air, allowing rapid galvanic corrosion to occur.
Contact us
CEP Forensic has a team of seasoned and specialized experts in materials, metallurgy, and mechanical engineering to offer clear answers to your questions in the management of your claim file.